Viele Autofahrer reparieren Motoren ihrer Autos auf dem Boden der Garage oder auf einer Werkbank. Dies ist immer unpraktisch, da ständig Gewichte angehoben und ein sperriger Zylinderblock oder Zylinderkopf gekippt werden. All diese Faktoren führen zu einer übermäßigen Ermüdung eines Autofahrers und einer Verschlechterung der Qualität der Motorbaugruppe. Um ihre Arbeit zu erleichtern, haben die Handwerker viele hausgemachte Kippkonstruktionen für den Motor entwickelt.
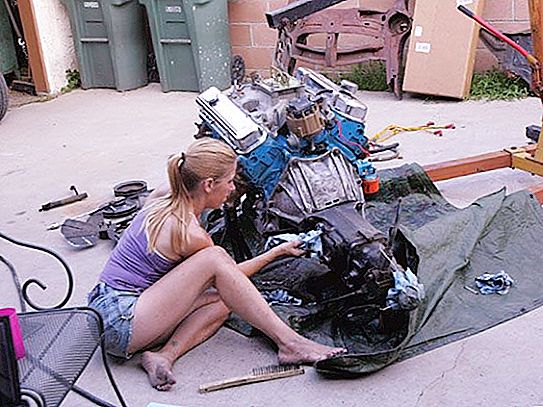
Optionen für hausgemachte Tilter-Designs
Tatsächlich gibt es nicht viele Optionen. Im Westen sind komplexe und sperrige hausgemachte Konstruktionen bekannt, wie ein Kranträger, fast mit hydraulischen Antrieben.
Unter häuslichen Bedingungen montieren Autofahrer die einfachsten Konstruktionen aus dem, was zur Hand ist. Aus hausgemachten Kippern für den Motor sind Versionen mit zwei Stützen und Auslegern des Designs bekannt. Am einfachsten herzustellen ist das neueste Design. Seine Eigenschaften reichen für die Überholung fast aller Motoren eines Autos mit einem Gewicht von 150 bis 250 kg aus.
Zeichnungen und Gesamtabmessungen
Bevor mit der Herstellung des Geräts fortgefahren werden kann, müssen die vorhandenen Muster der Ständer für die Motorreparatur eingehend untersucht werden. Die Probe wird für die dringenden Bedürfnisse eines Amateurmechanikers ausgewählt. Wir bewerten die Verfügbarkeit von Materialien und Größen, um bequem in einer kleinen Garage arbeiten zu können. Das Gewicht der zulässigen Last richtet sich nach dem Motortyp, der repariert werden soll.
Nach den Ergebnissen der Untersuchung bestehender Strukturen wurde eine Entwurfszeichnung der optimalsten Version des Cantilever-Kippers entwickelt. Die Gesamtabmessungen im Diagramm sind in Millimetern angegeben.
In der Skizze entsprechen die Bezeichnungen D 60 und D 52 einem Durchmesser von 60 und 52 mm.
Materialien für die Herstellung
Aufgrund der Tatsache, dass der Kipphebel für den Motor unter rauen physischen Belastungsbedingungen arbeiten muss, die mit dem Gewicht des Motors verbunden sind, werden hohe Anforderungen an die Materialien gestellt.
Folgende Materialien werden zur Herstellung verwendet:
- quadratisches Stahlprofil 70 x 70 mit einer Wandstärke von 3 mm und einer Länge von 3 m;
- Stahlrohr mit einem Außendurchmesser von 60 mm, einem Innendurchmesser von 53 mm und einer Länge von 245 mm;
- Stahlrohr mit einem Außendurchmesser von 47 mm und einer Länge von 480 mm;
- Stahlkanal mit einer inneren Seitenbreite von 70 mm, einer Wandstärke von 3-4 mm, einer Länge von 280 mm;
- Flansch zum Verschrauben mit dem Motor - 1 Stck.
Werkzeuge und Hardware für die Montage des Ständers
Um die Metallstrukturen aus einem Stahlkanal und einem quadratischen Profil zu verbinden, ist ein Schweißgerät erforderlich, mit dem mit einer Elektrode mit einem Querschnitt von mindestens 3-4 mm gearbeitet werden kann. Zusätzlich benötigen Sie zum Schneiden eine Schleifmaschine mit einer Schneidscheibe für Metall mit einem Durchmesser von 115-125 mm. Um eine Schraubverbindung von vorgefertigten Teilen zu gewährleisten, ist ein Bohrer erforderlich, der mit einem Bohrer mit einem Durchmesser von bis zu 14 bis 20 mm arbeiten kann Für die Montage der Struktur werden auch M12-Schrauben benötigt.
Sie benötigen außerdem eine Reihe von Feilen zum Schneiden von Graten und unebenen Kanten, um Fehler beim Metallschneiden zu beseitigen. Es tut nicht weh, vor dem Lackieren ein Schmirgelleinen zu kaufen, um die Oberfläche von Rost zu reinigen.
Motorkipphebel
Der erste Schritt ist das Schneiden des Kanal- und Quadratprofils gemäß der Skizze. Als nächstes wird ein vertikaler Ständer aus einem Profil hergestellt und aus einem Kanal mit einem Quadrat verschweißt. Anschließend wird die Struktur mit Metallschrägen verstärkt, die aus Teilefetzen hergestellt werden können.
Danach wird aus dem geschnittenen quadratischen Profil die Basis geschweißt - der Kippständer für die Motorreparatur. An der Stelle der Verschraubung mit der Basis des vertikalen Racks werden Vorarbeiten durchgeführt, Stahlbuchsen eingesetzt und geschweißt, um die Struktur zu stärken.
Fahren Sie dann mit der Endmontage des Motorkippers fort. Der Ständer ist durch Schweißen und M12-Schrauben mit dem Ständer verbunden.
Ein horizontales Rohr mit einem Außendurchmesser von 60 mm und einem Innendurchmesser von 52 mm wird durch Schweißen am vertikalen Ständer befestigt. In diesen Teil wird eine horizontale Achse eingefügt. Es kann aus einem Stahlrohr mit einem Durchmesser von 47 mm mit einem geschweißten Flansch zum Verschrauben des Zylinderblocks oder Zylinderkopfes bestehen.
In der horizontalen Achse können Sie alle 45 ° entlang des Radius Löcher bohren, um die Position im Raum mit den Stiften zu fixieren, nachdem Sie den angebrachten Motor auf den gewünschten Winkel gedreht haben.
Der zusammengebaute Motorkipper sollte gereinigt und grundiert und dann mit Nitro-Email lackiert werden, um Metallkorrosion zu verhindern und die Qualität der Überholungen zu verbessern.
Wenn keine zusammenklappbare Konstruktion erforderlich ist, kann der vertikale Ständer nicht durch Verschrauben, sondern durch Schweißen am Ständer befestigt werden. Danach können Sie mit dem Gerät mit schwereren Motoren arbeiten. Wie Sie wissen, kann 1 cm der Schweißnaht 100 kg Belastung aushalten. Und das ist viel. Sie können sich vorstellen, welcher Art von Ladung eine hausgemachte Einheit, die über alle Gelenkkanten gekocht wird, standhalten kann. Es kann sogar zu einem Kippen des YaMZ-Motors kommen.
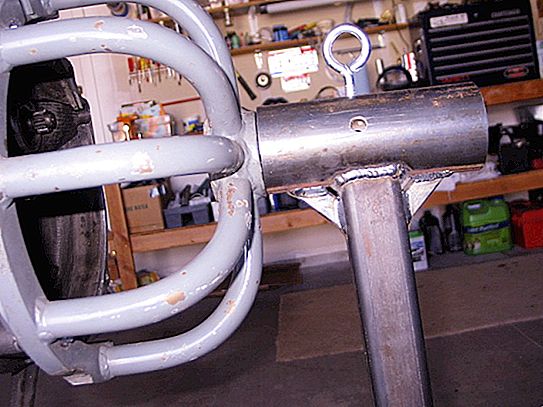